Louise Crocker and Tony Fry from the National Physical Laboratory looks at the role of metrology in developing new materials with improved resistance
The efficiency and service life of high-value industrial components can be critically impacted by solid particle erosion, particularly at high temperatures (HTSPE). Developing new materials with improved resistance to HTSPE can lead to major improvements in the efficiency of plant and aero-engines. The development and/or implementation of new materials and coatings has been hampered by the lack of traceable measurement in HTSPE testing, the assessment of the erosion resistance of materials and surface treatments has to date been largely empirical and non-standardised. The erosion rate is calculated through measurement of the rate of change in mass or volume as a function of the mass of erodent particles. To achieve this within conventional HTSPE testing the sample is cooled periodically during the test, removed from the apparatus and mass change and/or the volume of the erosion scar measured. The sample is then reinserted into the apparatus, heated and the test can proceed. This leads to misalignment errors in repositioning the sample, thermal cycling, and long test times due to heating and cooling.
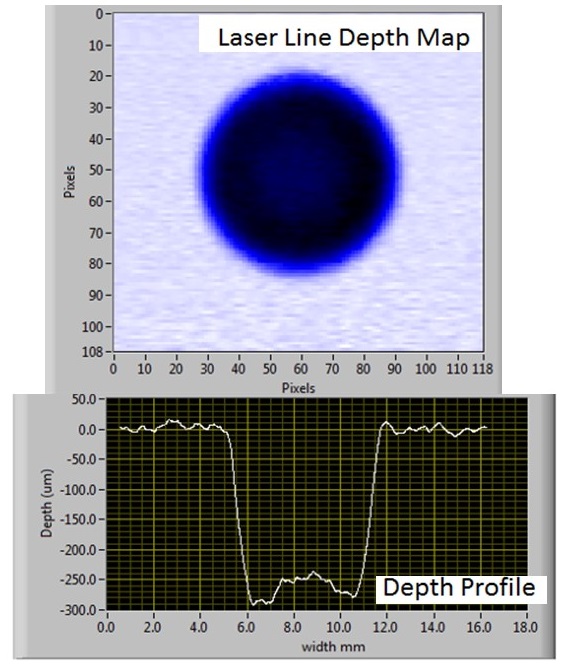
METROSION initiative
A European initiative – METROSION – was instigated to enable a step change in the monitoring and control of HTSPE testing providing traceable measurements and improved tests. As part of this project, the National Physical Laboratory (NPL), the UK’s National Measurement Institute, developed a new HTSPE facility extending the speed and temperature range which can be measured and incorporating in situ measurements, the first time this has been implemented worldwide. Within the project 3 novel in situ measurement systems have been designed, built and validated to measure the mass and volume change of the sample and the particle velocity and velocity distribution. This is the first time all 3 measurements can be made during the test and at high temperature, greatly reducing the uncertainties relating to specimen positioning and decreasing the time needed to generate the erosion curves.
To perform the in situ mass measurement the rig has been designed to include a precision balance. A method of diverting the gas flow has been implemented which allows the mass to be measured between erosion intervals. Whilst the gas stream is diverted, a laser triangulation system developed at NPL can be used to scan the surface of the sample and measure the geometry of the erosion scar and thus calculate the volume change of the sample surface. It currently takes approximately 30 minutes to acquire the images required to generate a height map with the necessary resolution for precise volume change measurement, see Figure 1. These in situ measurements have enabled an HTSPE test to be conducted in as little time as 2 hours for purely mass change measurements and ~6 hours for both mass and volume change measurements. Conventionally this would have taken ~3 days of effort.
To be able to relate laboratory results to actual operating conditions, erosion tests should be conducted using representative particle velocities to reduce uncertainty in measured erosion rates and to account for any mechanism changes as a function of velocity and temperature. To realise the measurement of velocity and velocity distribution as a function of particle size, an in situ optical method was developed at the Technical University of Denmark (DTU), which enables high-speed particle image velocimetry to be conducted at high temperature, in a cost effective manner. The new method uses pulsed background lighting and high-speed image capture of moving particles which allow imaging and measurement of fast moving particles, see Figure 2. The velocity of each particle is calculated from a displacement of the centre of mass. Integration of this sensor to existing test rigs is possible and provides, for the first time, full measurement of the particle velocity distribution as a function of particle size across the gas stream.
Whilst this method is capable of providing size and 2D shape information as well as velocity measurements, to fully understand the erosion process, a more detailed method of particle sizing is required. The erosive particles can be characterised in terms of their geometry and size, using a range of different measurement techniques, such as laser light scattering. PTB, Germany’s National Metrology Institute, has developed, as part of this project, a method to describe the shape of the particles using mathematical descriptors based on X-ray computed tomography measurements of the particle geometry. These descriptors can be used with the in situ velocity measurements to generate velocity models for predicting the distribution of particle velocities as a function of their size, geometry and aspect ratios. This can be used in erosion models to provide more realistic predictions of damage accumulation and relate the HTSPE test results to real world conditions.
Further developmental and validation work on the measurement methods described is progressing with the aim to provide the industry with a traceable HTSPE test through the NPL Measurement Services by early 2018. Further details on the Metrosion project can be obtained from NPL project website.
Louise Crocker
Senior Research Scientist
Tony Fry
Principal Research Scientist
National Physical Laboratory
Tel: +44 (0)20 8943 6220
tony.fry@npl.co.uk
www.npl.co.uk
Please note: this is a commercial profile