A design for agricultural robots named ‘FAIRY’ – Flying Aero-robots based on Light Responsive Materials Assembly – could aid artificial pollination
Due to the increasing challenges of the climate crisis, the use of technology in nature and food production, such as agricultural robots, is increasing.
One team from Tampere University have taken a special approach to this research – looking at how to make smart material fly in tiny devices they have coined as ‘FAIRY’.
The inventors aim with this research for millions of these artificial dandelion seeds to one day carry pollen, to be dispersed by natural winds and directed by light toward specific areas with trees awaiting pollination.
“An important step towards realistic applications suitable for artificial pollination”
This is one of the first projects to make these materials fly
The artificial fairy has a tiny dandelion seed-like structure with several biomimetic features. Using stimuli-responsive polymers, these next-generation small-scale, wirelessly controlled soft-bodied agricultural robots can fly by wind and can be controlled by light.
Due to the fairy’s high porosity (0.95) and lightweight (1.2 mg) structure, it can easily float in the air directed by the wind.
It also has a stable separated vortex ring generation that enables long-distance wind-assisted travelling.
Researcher Hao Zeng said: “Superior to its natural counterparts, this artificial seed is equipped with a soft actuator. The actuator is made of light-responsive liquid crystalline elastomer, which induces opening or closing actions of the bristles upon visible light excitation.
“The fairy can be powered and controlled by a light source, such as a laser beam or LED.”
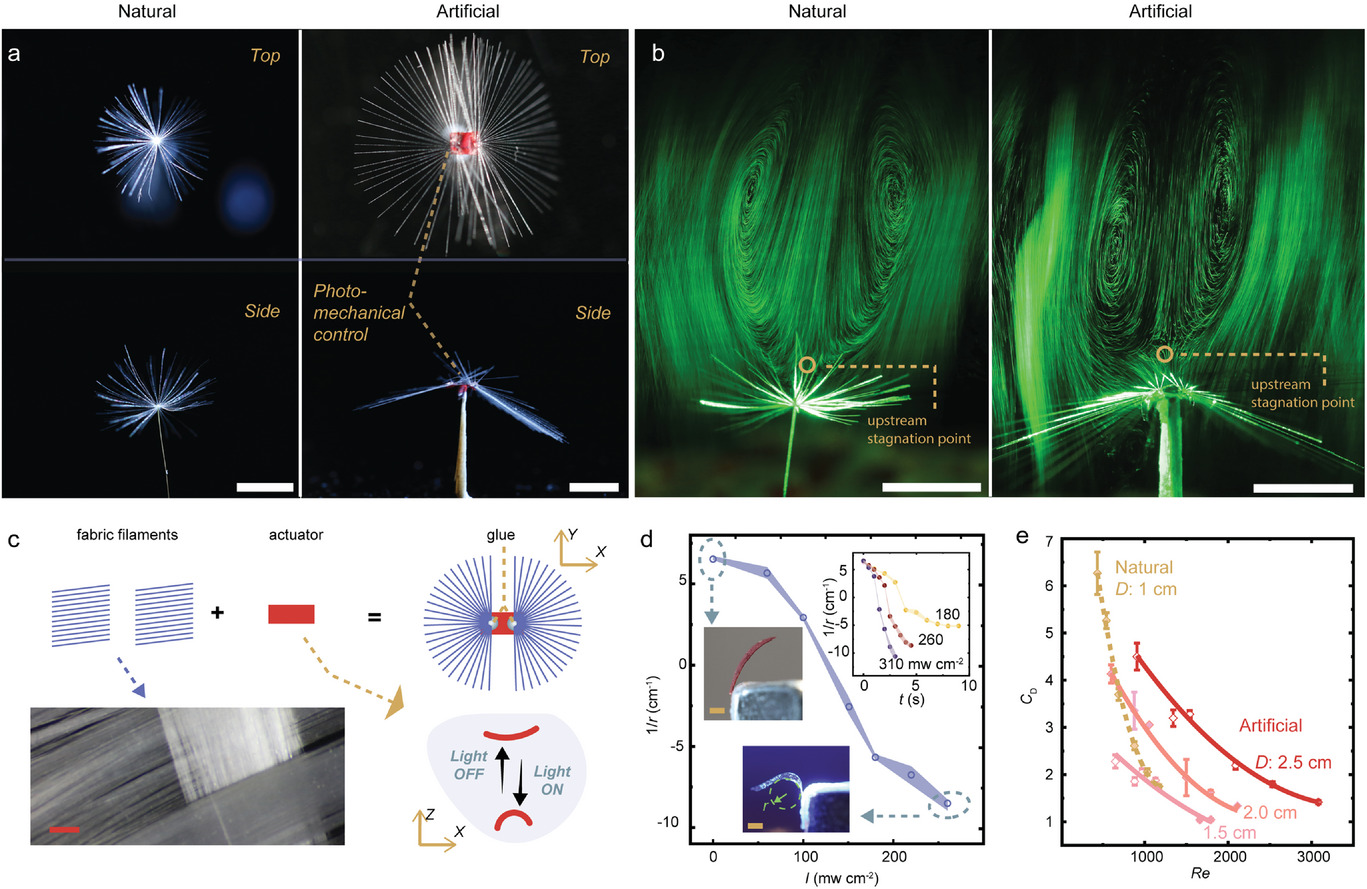
© https://onlinelibrary.wiley.com/doi/10.1002/advs.202206752
While light changes the shape of the structure, it can also adapt manually to wind direction and force by changing its shape. A light beam can also be used to control the take-off and landing actions of the polymer assembly.
GPS, sensors, and biochemical compounds may be a reality for this device
By improving the material sensitivity to enable the operation of the device in sunlight, this device can be solar-powered and will one day be able to carry micro-electronic devices such as GPS and sensors as well as biochemical compounds.
Zeng added: “It sounds like science fiction, but the proof-of-concept experiments included in our research show that the robot we have developed provides an important step towards realistic applications suitable for artificial pollination.
“This would have a huge impact on agriculture globally”
“This would have a huge impact on agriculture globally since the loss of pollinators due to global warming has become a serious threat to biodiversity and food production.”