Nuria RodrÃguez López talks us through the climate necessity of the ReSiSTant project, which is a Horizon 2020 EU NMBP-Pilot Project, to reduce the environmental impacts of aircrafts
ReSiSTant stands for Large Riblet Surface with Super Hardness, Mechanical and Temperature Resistance by nanofunctionalization. It is a Horizon 2020 EU NMBP – Pilot Project, which is developing new nanofunctionalized and optimised riblets’ surfaces to be applied in two real demonstrators related to aircraft turbofan engines and industrial compressors.
Riblet surfaces consist of very small (2-100 microns) streamwise grooved surfaces. They are the only aircraft passive drag reduction system already mature for application in the next-generation aircrafts. These surface structures could achieve up to 8% of drag reduction under turbulent flow conditions. Hence their potential for energy saving as well as weight and noise reduction is enormous in aircraft industry as well as for enhancement of generators’ performances in wind and gas turbine industry.
In order to maximise the benefits related to the application of riblet’s surfaces in drag or even noise reduction, ReSiSTant project is improving riblet’s features considering new materials and additional surface functionalization (nanostructures and nanoparticles). Nanocoatings have become an integral part of various end-user industries, ranging from manufacturing to medical & healthcare. End-user industries (such as ReSiSTant target industries) have started to be aware of the advantages of using nanotechnology in combination with conventional paints and coatings.
In this context, ReSiSTant project has defined two relevant industrial demonstrators to validate this technology: aircraft turbofan engines and industrial compressors. The harsh working conditions are very challenging: high temperatures, high abrasion and erosion, heavy corrosion, etc. so technology validation for the optimised riblet’s coatings in relevant environment is essential.
The four-year project ReSiSTant, launched in 2018, is optimising the performance of aircraft turbofan engines and industrial compressors while reducing environmental impact. By the end of the project in December 2021, the consortium will deliver optimised coated riblet’s surfaces on target parts for both industrial demonstrators and pilot lines for the production of these parts.
Project overview and first nanotechnology results:
During the project, riblet’s design is determined based on the calculation of geometries, numerical simulation of the riblet-effect and the selection of number of riblets and their position. Secondly, several tests are performed for aircraft turbofans and industrial compressors. These tests are performed with and without riblets and the results are compared to the previous ones performed using Computational Fluid Dynamics (CFD). In parallel, several nanocoating techniques are analysed, both considering materials definition and deposition technology. Based on these conclusions, riblet’s material, nanofunctionalization and nanostructures for both demonstrators (aircraft turbofans and industrial compressors) are developed. Afterwards, the final selection is performed regarding material and application technology for demonstrators, riblet’s structures and type of nanofunctionalization and nanostructures. At last, riblet’s coated parts for demonstrators are produced and tested on industrial demonstrators. Then, in-service test operation of demonstrators and business case evaluation are carried out in order to determine the performance of each demonstrator and to evaluate their business potential (Figure 1).
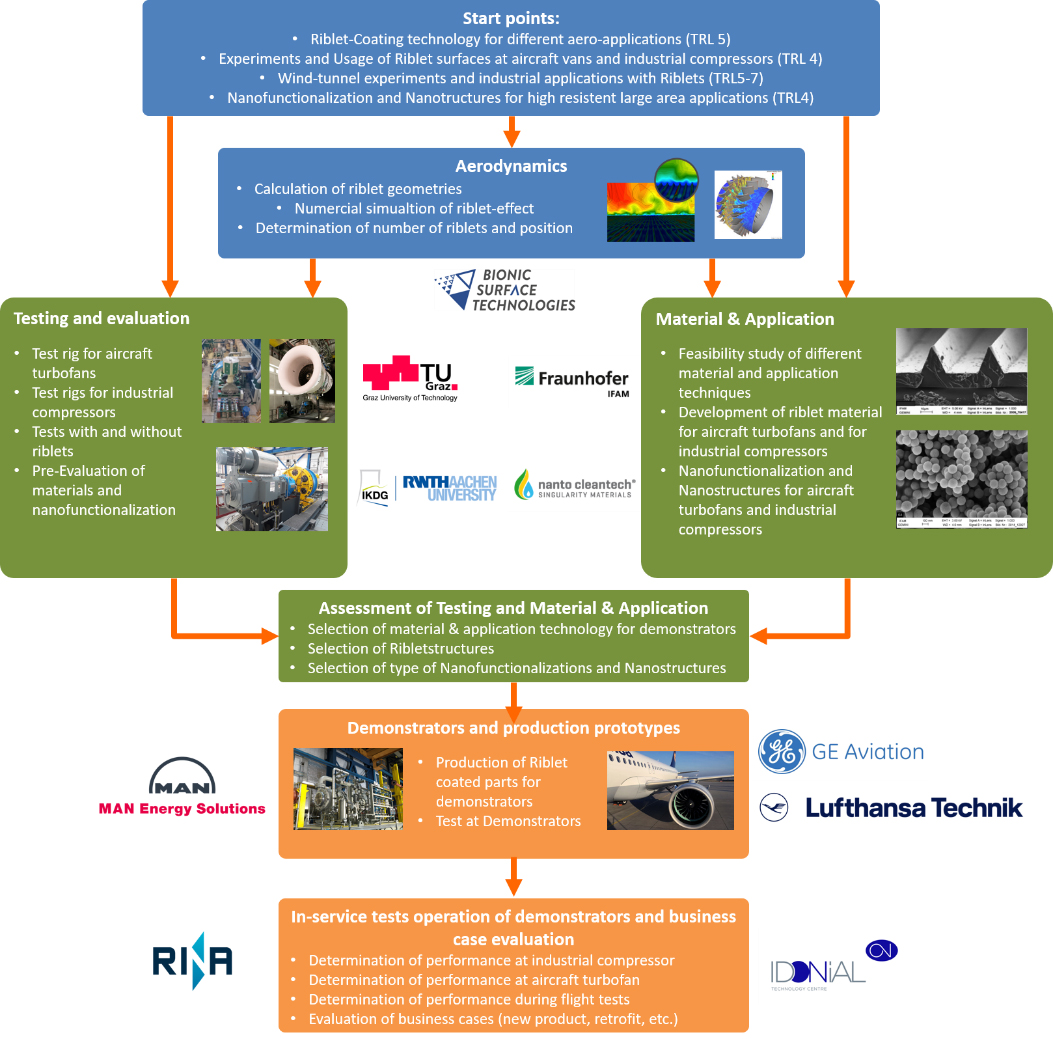
Hence, the micro-structures (riblets) are intended to reduce friction on the surface of the target part. Regarding the nanotechnology developments, the riblets are covered by additional nanostructures to give the surface further functionalities (nanocoating) such as easy to clean properties or erosion resistance (Figure 2).
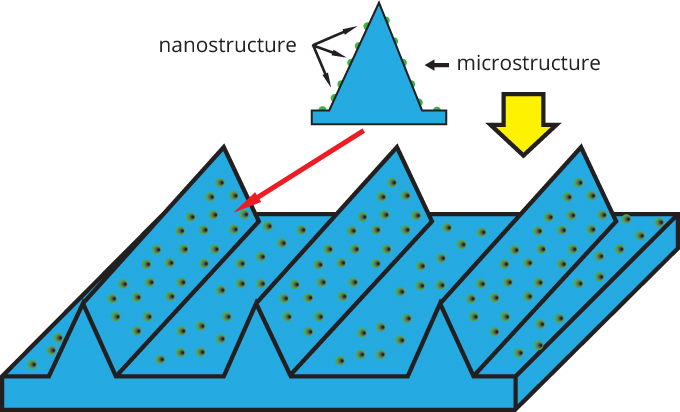
To enable the usage of such micro- and nanostructures, special development on the surface material for better durability in rough conditions has been done. Implementation of nanoparticles such as silica to obtain nanofunctionalized surfaces for better resistance in rough conditions has been carried out. Microstructured heat-resistant surfaces have been developed and are available for tests at project partners’ premises (Figure 3). For the formulation of the coating silanol-functional and silazane- functional resins have been selected to achieve high-performance coatings with good flexibility and heat resistance. For improvement of heat resistance special pigments have been examined and evaluated to gain outstanding resistance to temperatures up to 1000°C. The incorporation of the selected particles and the dispersion partly to nano-scale have been developed and assessed.
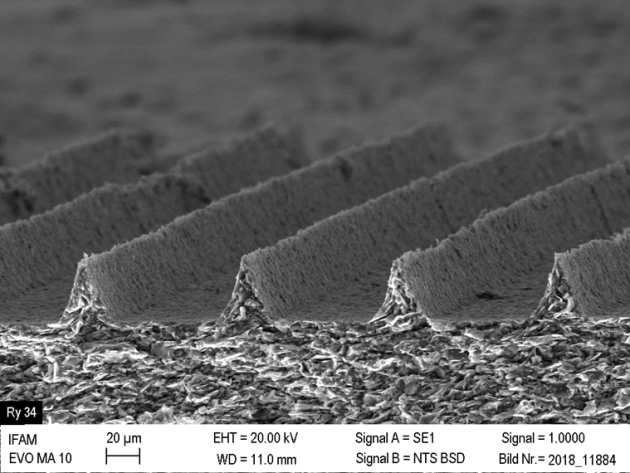
Market impact/Impact in Europe and Industrial demonstrators:
ReSiSTant project directly impacts on three key sectors in Europe: nanocoating, aircraft and industrial compressors. For the case of nanocoating, it is forecasted that European market will be the second one in 2026, following North America. Likewise, aircraft market offers very promising forecasts in relation to the increase of European flights and passenger counts at European airports. It positively impacts on the global businesses for aircraft engines and maintenance component repair and overhaul services (including spare parts sales). Finally, the global industrial gas compressor market also estimates an important growth on the following years as well as gas turbine for energy production.
ReSiSTant demonstrators are led by relevant industrial companies on aircraft and industrial compressors sectors, thus project improvements will notably impact in Europe. It will be translated into environmental benefits thanks to the reduction on fuel consumption and carbon emissions as well as into an economic growth.
The final stakeholders’ event will take place in 2021 where final project results will be presented to the community. To learn more about upcoming deliverables and project events, please visit our website and subscribe to our newsletter.
This project has received funding from the European Union’s Horizon 2020 research and innovation programme under grant agreement No 760941.
Please note: This is a commercial profile