Prof. Masahiro Kamitani from the Department of Chemistry at Kitasato University, Japan, introduces the silicone materials and recent achievements in their production process with an earth abundant iron
Silicone (not silicon) materials are silicon-based polymers in the form of oils, rubbers, and resin; these are used in a wide range of applications, e.g., cosmetics, kitchenware, contact lenses, etc. (Figure 1).
Compared to carbon-based polymers like polyethylene (one of plastics), these silicon-based polymers have excellent properties, especially in terms of high heat proofing and weather resistance. Nevertheless, the market size of silicones, as well as the range of their applications, is far inferior to that of carbon-based polymers mainly because of the high cost of silicone materials owing to the issues associated with their production.
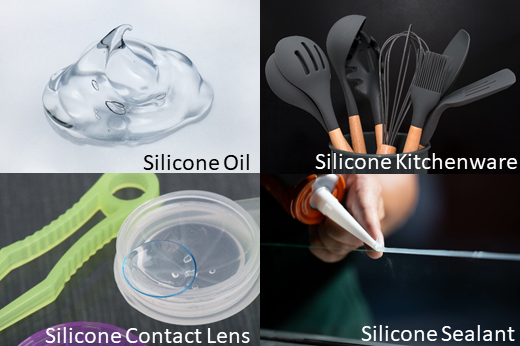
Current silicone production process
The majority of carbon-based synthetic polymers (plastics), such as polyethylene (PE), polypropylene (PP), and polystyrene (PS), are prepared mainly from limited fossil resources; on the other hand, the major silicon resource is sand, which is highly abundant on Earth. The chemical bonds in silicone materials are the Si-O-Si bonds in the main chain and Si–C bonds in the side chain. The Si-O-Si bonds are ubiquitous in natural materials, e.g. in quartz and sand as silica (SiO2). Thus, the heat-proof and weather-resistant properties of silicones are derived from the robust main framework (Si-O-Si), which is similar to silica (the principal component of glass).
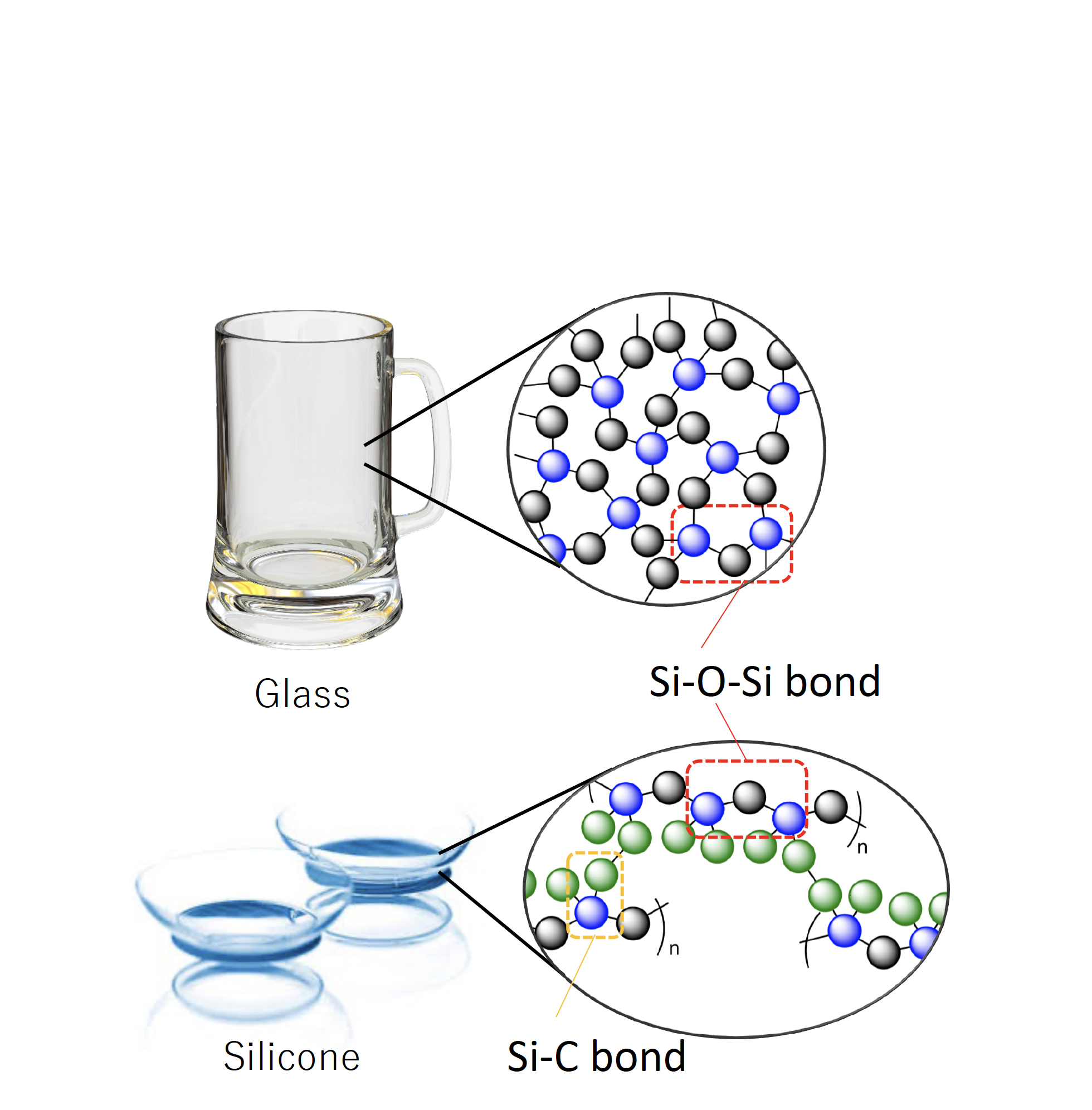
The Si–C bond does not exist in nature and is prepared in industry and research laboratories. In other words, all silicone materials in the world are produced by artificial chemical processes. Hydrosilylation is one of the major chemical reactions used for the formation of the Si–C bonds from raw materials (hydrosilane and alkene). Pt-based catalysts, known as Karstedt catalysts, are extremely active for hydrosilylation and are used in industrial processes. However, Pt is well dispersed in silicone products after the reaction, and becomes mostly unrecyclable. The amount of unrecyclable Pt is estimated to be ~3% of the annual worldwide production (A. J. Holwell, Platinum Metal Review 2008, 52, 243-246), which increases the cost of silicone production.
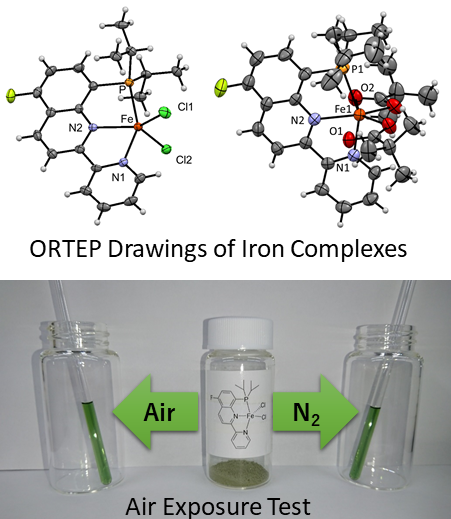
Inexpensive iron catalysts as alternation to platinum catalysts
Bolm called the thriving research on the development of iron catalysts “a new iron age” (C. Bolm, Nat. Chem. 2009, 1, 420); therefore, iron has been actively investigated as a synthetic catalyst to replace the more expensive precious metal (e.g. platinum) catalysts that are widely used for chemical processes. Iron is the most abundant transition metal on planets, and unlike precious metals, are relatively less expensive and less toxic.
The replacement of platinum catalysts for silicone production with an iron catalyst has been extensively studied over the past few decades. Although some iron catalysts with activities comparable to those of platinum catalysts have been reported to date, they are not suitable for practical use owing to their air-sensitivity. Other iron catalysts were air-stable, but exhibited lower activity. Thus, there is a trade-off between catalyst stability and activity, and it is very difficult to achieve both high stability and activity simultaneously, which is important to design an iron catalyst for practical use.
Stable but Active Iron Catalysts
Recently, our research group developed air-stable iron complexes for various catalytic reactions (Kamitani et al., Bull. Chem. Soc. Jpn. 2018, 91, 1429-1435) and one of them is now on sale from a private company. The stability of these catalysts was confirmed by an air exposure test (Figure 3).
The series of iron complexes exhibited catalytic performance for hydrosilylation, i.e. its turnover number (TON = 480,000) and turnover frequency (TOF > 10,000/h) are the highest values reported for iron catalysts (Kamitani et al., Chem. Lett. 2019, 48, 1196-1198). We are currently conducting further developments for more useful and practical applications. This study was financially supported by the New Energy and Industrial Technology Development Organization (NEDO, Japan) project (PL: Dr. Kazuhiko Sato, AIST, Japan). We also thank Dr. Hiroshi Nakazawa (OCU, Japan) for supporting the NEDO project.
Please note: This is a commercial profile