Prof Mikael S Hedenqvist and Dr Oisik Das from KTH Royal Institute of Technology in Sweden explain self-reinforced gluten polymers and why they are a step towards a true biocomposite
Bio-based polymer products are getting an increased amount of attention due to a paradigm shift in manufacturing towards sustainability. Wheat gluten (WG) is one such natural polymer that is a cereal-based protein produced as a coproduct of food industries. WG is attractive because it satisfies the growing need for polymers from renewable resources and exhibits acceptable mechanical properties. WG is a cohesive material with good oxygen barrier properties and can be moulded to various shapes such as films, foams and solids.
However, WG suffers from inherent disadvantages that hinder its widespread application. The mechanical properties of WG are inferior to that of the synthetic counterparts and they are also susceptible to moisture, microbes and fire. To remedy these issues, it is critical to identify reinforcements that are not only bio-based, but also to enhance WG’s performance properties.
Biochar, which is a solid pyrolysis product of biomass, was found to be a potent reinforcing material for synthetic polymers (1). During pyrolysis (heating at high temperatures, ca. 500-900 °C with limited O2), the volatiles from biomass evolve, creating a porous and carbonaceous material (formed by gradual condensation of carbons into aromatic clusters). During processing, the molten polymer flows through the biochar pores – forming a mechanical interlocking like the ‘Velcro effect.’ The biochar, made at high temperatures also has remarkable fire resistance (1). Hence, biochar is a reinforcement in polymeric materials which enhances both mechanical and fire properties.
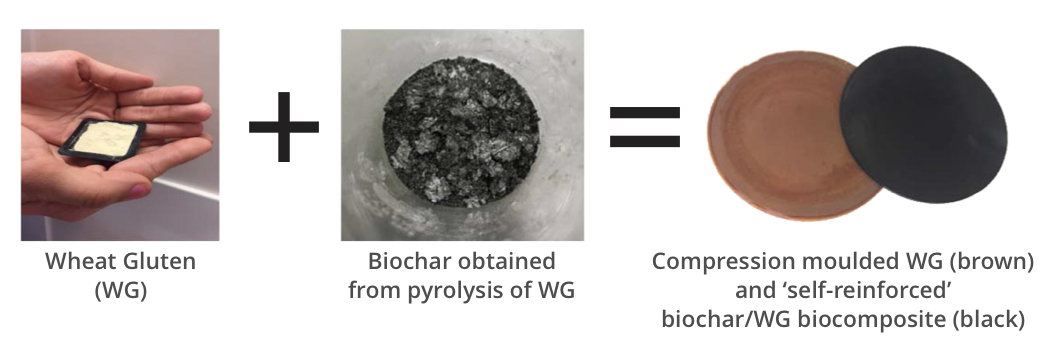
Earlier studies have shown that it is possible to make biocomposites from various organic materials by utilising the fact that it can be converted to biochar that is retrieved from the material undergoing pyrolysis (2). Therefore, the application of the same method on materials from other sources is a possible approach to obtain innovative biocomposites. The polymeric materials division at KTH Royal Institute of Technology pyrolysed WG and the biochar obtained was added to the WG polymer itself to create a novel and a true homo-biocomposite (Figure 1).
This ‘self-reinforced’ biocomposite’s components are derived from the same source but undergo different treatments for the same material to reinforce itself. It is envisaged that this biochar/WG composite would be simultaneously mechanically strong, fire and moisture resistant giving rise to a new class of polymeric materials.
- Das, O., Kim, N-K., Kalamkarov, A.L., Sarmah, A.K., Bhattacharyya, D., 2017. Polymer Degradation and Stability. 144: 485-496.
- Das, O., Kim, N-K, Hedenqvist, M.S., Lin, R.J.T., Sarmah, A.K., Bhattacharyya, D., 2018. Environment Management Journal. DOI: https://doi.org/10.1007/s00267-018-1033-6.
Please note: this is a commercial profile
Prof Mikael S Hedenqvist
Dr Oisik Das
Department of Fibre and Polymer Technology Polymeric Materials Division
School of Engineering Sciences in Chemistry, Biotechnology and Health
KTH Royal Institute of Technology
Stockholm, Sweden
Tel: +46 706 507 645 (M.H.)
+46 790 469 886 (O.D.)