Jen-Yuan (James) Chang, Professor at the Department of Power Mechanical Engineering at the National Tsing Hua University, Taiwan, tells us why the Adaptive Robotic Gripper is the route to grasp the wave of Industrial 4.0 and smart manufacturing
In Industry 4.0 applications, being able to hand and grasp objects of any shape precisely and reliably are essential in smart manufacturing operations. In this article, several essential considerations concerning the development of a robotic gripper are discussed and illustrated by an adaptive robotic gripper developed through research funded by Ministry of Science and Technology, Taiwan. Possibilities of such adaptive robotic gripper with artificial intelligence are discussed in the context of applications in smart manufacturing.
With the advancement of technologies and increasing demand for grasping objects automatically, robots have been widely used in industrial, commercial and even home applications. For applications in daily life and in the smart manufacturing environment, a robotic gripper, which could be used universally to grasp objects of any shape, has become its engineering importance. Featuring high accuracy, high repeatability and strong gripping force, an industrial robotic gripper which can be attached to a robot’s end-effector is commonly designed to possess a single degree of freedom actuation, resulting in simple opening and closing operations. Although it has the aforementioned advantages, it is hard to adapt such design to different objects. In present practice with such an of actuation design, when a target object is changed, a different adaptor to suit for the object’s shape is required. As such, to reach the flexibility of grasping, changing adaptor in this single degree of freedom gripper is necessary.
Human’s Hand
The most dexterous gripper currently available is the Human’s Hand, which was demonstrated by researchers from Johns Hopkins University. To mimic the characteristics of a human hand, a multiple degrees of freedom humanoid robotic hand has been widely researched with efforts placed on the minimisation of actuators, such as motors (the mechanical structures in a limited space). Although its dexterity is satisfactory, the cost is extremely high and is not sufficiently compliant to adapt to a different shape. To offer compliance, some soft materials have been used in the robotic hands as well, the best example of which was demonstrated by researchers from Harvard University. Although a soft gripper can offer good compliance and adaption to shapes, its accuracy and payload, in fact, are very limited due to soft materials.
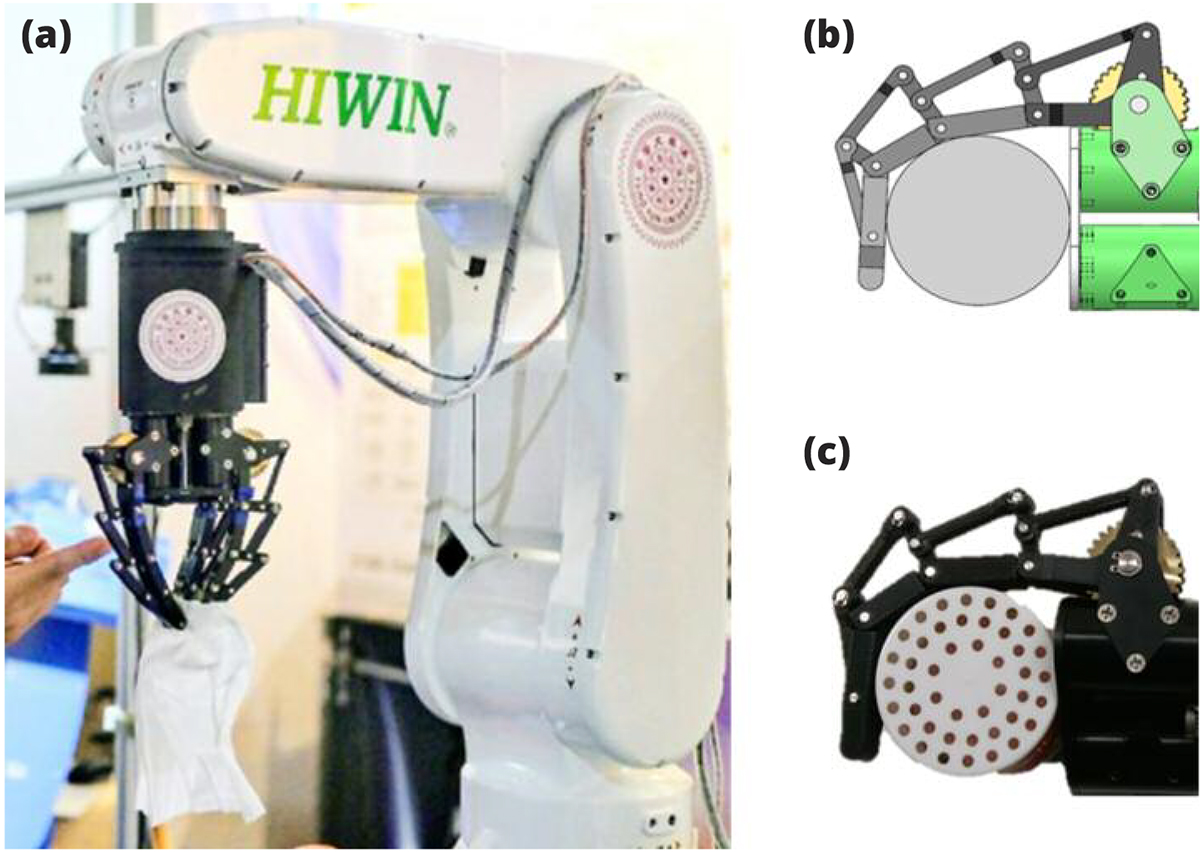
To reduce the driving sources, such as the number of motors used but to keep or even improve the adaptability of the gripper, the adaptive robotic gripper as shown in Figure 1 has been developed by Professor Chang’s research group from the Department of Power Mechanical Engineering at National Tsing Hua University, Taiwan. Through funding support from the Ministry of Science and Technology, Taiwan, the research results were technology transferred to HIWIN Technologies Corp. for the development of commercial adaptive grippers that can be used in smart manufacturing applications. As illustrated in Figure 1(b) and Figure 1(c), the so-called compliance or adaptation can be achieved by the multiple four-bar linkages packed in series.
Each linkage can be assumed to be rigid to be able to transmit a strong gripping force to grasp an object. With the well-engineered design of the mechanism of the four-bar linkages in series, adaptation and compliance can be achieved. Based on the four-bar linkage in the series design concept, Professor Chang’s group have developed mathematical functions for each adaptive gripper finger joint to allow the development of adaptive robotic gripper for different service and industrial robotic applications.
With the analytical model and mechatronics integration, the fingers of this NTHU adaptive gripper not only offer compliance and adaptation performance similar to the human finger but they also provide satisfactory engineering performance in terms of receptivity and reliability. The NTHU adaptive gripper offers a wide range of payload performance. It can easily lift up and hold a 3 kg object, as well as to pinch a piece of tissue paper, as illustrated in Figure 1(a).
Mimicking the human hand in which dexterity is achieved primarily by the thumb, the index and the middle fingers with the ring finger and little finger are pretty much used to help hold objects. Certainly, three fingers designed with the series four-far linkages are adopted in this NTHU adaptive gripper to save on the cost but also offer the same performance and dexterity. Each finger is placed evenly by 120 degrees and is attached to the controller unit of the gripper. However, the adaptation of the gripper is further extended by allowing each finger to rotate independently at desired orientations.
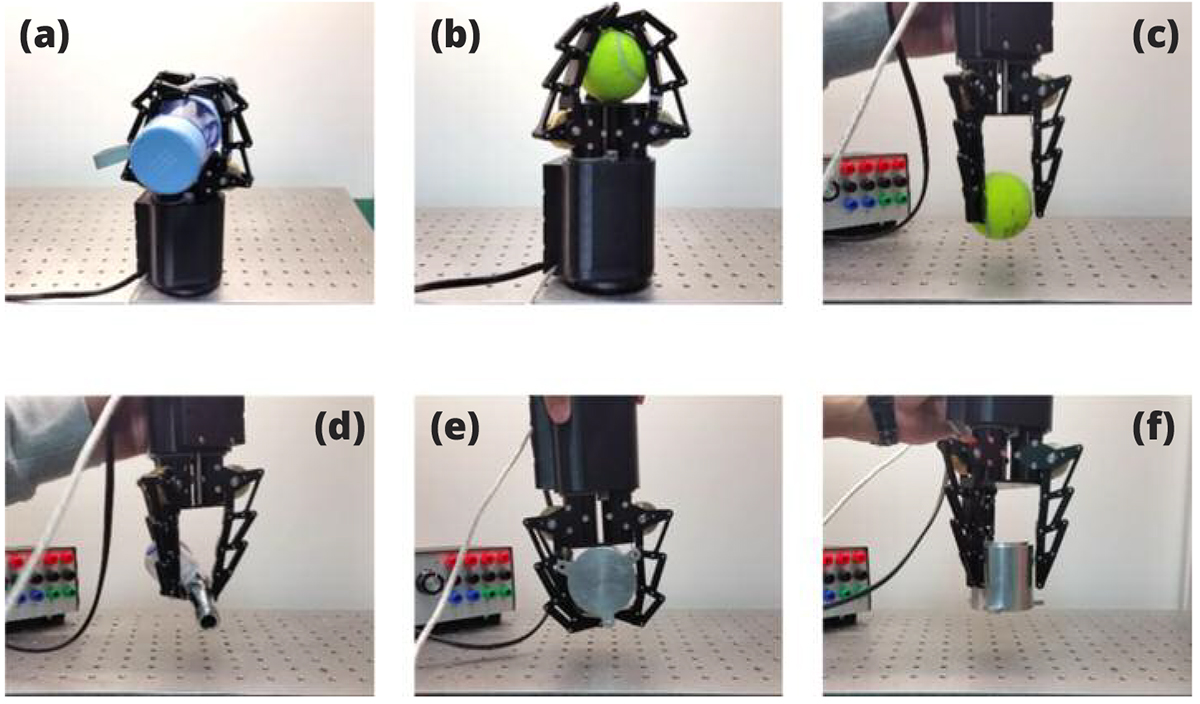
As demonstrated in Figure 2, the orientation of the gripper finger can be adjusted according to the shape of the object. Such adaptation is not possible in the present robot gripper, which certainly offers the possibility of eliminating a change of adaptor in the present industrial robotic gripper. Should such a dexterous adaptive robotic gripper be integrated with the machine vision, machine learning and artificial intelligence (AI), the intelligent grasping operation can truly be achieved in smart manufacturing, as well as in Industry 4.0 applications.
Jen-Yuan (James) Chang
Professor
Department of Power Mechanical Engineering
National Tsing Hua University, Taiwan
Tel: +886 3 574 2498
jychang@pme.nthu.edu.tw
http://www.pme.nthu.edu.tw/files/14-1265-74003,r4027-1.php?Lang=e
*Please note: This is a commercial profile