Two scientists from Teysha Technologies discuss how organic material can now be turned into a viable plastic substitute
In this interview, we talk to two scientists from Teysha Technologies, Prof Karen L. Wooley, Chief Technology Officer and Dr Ashlee A. Jahnke, Project Research Scientist about solving the plastic problem with biopolymers, including how organic biomass can now be turned into a viable plastic substitute.
As policymakers continue to crack down on plastics, with the EU Parliament recently approving a ban on single-use plastics, businesses are increasingly under pressure to source earth-friendly bioplastics for their products.
Can you tell us about the latest developments in biopolymers?
Karen: Over the past couple of decades, we’ve become keenly aware of the potential negative impacts that may occur for polymer materials that persist beyond their useful lifetime. This has led us to consider the full lifecycle of plastics at the initial design stage. One way of addressing this is by building polymers from natural products so that they are capable of degradation to regenerate the natural-product building blocks.
Ashlee: This kind of technology is truly more of a platform than a single polymer system, providing inherent versatility in the properties that can be achieved. It can be thought of as a plug-and-play system where various modified natural-product monomers and various co-monomers can be used.
In addition to co-monomers, various additives can be used to modify the properties of the final polymer produced. This versatility allows for the formation of a variety of materials that can vary greatly in their thermal and mechanical properties.
How does this technology compare to existing petroleum-based polycarbonates?
Karen: A significant advantage of this kind of technology is the use of natural, sustainable feedstocks to generate polycarbonate materials with the ability to tune the physical, mechanical and chemical properties by controlling the chemistry, formulation and polymerization conditions.
Because natural building blocks offer higher chemical diversity than typical hydrocarbon sources, this method can be used to tune the degradation rates of intact material systems. Most current polycarbonates are prepared from hydrocarbon-based petrochemicals and achieve varied properties through molar mass control, crystallinity control and blending with other polymers, with fewer opportunities to fine-tune individual properties.
Moreover, the most common polycarbonate is poly(Bisphenol A carbonate), which generates bisphenol A (BPA) upon hydrolytic breakdown – for example, under the extreme conditions in a dishwasher. Since BPA has been implicated in several diseases, avoiding its use as a building block for engineering plastics is of high importance.
How can the polymers be tuned and what does this mean for things like durability and biodegradability?
Karen: The strength, toughness, durability and longevity of these polymers are dependent on the properties of the specific monomers used in polymerization and can be tuned for various applications. The material properties range from flexible to rigid, with degradation occurring over a period of weeks to years, and depending on the polymer composition and the environmental conditions.
Ashlee: These new kinds of polymers also have varied thermal stabilities depending on the composition and have degradation temperatures that are generally similar to but in some cases, lower than other polycarbonate and polyester materials. Another area to consider is how well biopolymers and their processing methods respond to additives, and whether they’re compatible with various dyes, scents, oils, plasticizers and nanoparticles.
The main mechanism of polymer degradation is through hydrolytic degradation, allowing for a breakdown in any environment containing moisture and does not require microbial activity, anaerobic conditions or industrial composting.
To determine the best disposal methods for a complete breakdown, we’re still measuring and testing full degradation profiles in various potential disposal conditions – like in waterways, landfills and composting.
What renewable sources can be used as feedstock to make these biopolymers?
Ashlee: This technology can use a wide variety of renewable, natural products for monomer feedstocks. The current focus is on the use of polyhydroxyl natural products, including those derived from starches, as well as agricultural waste products.
What kinds of material applications are these biopolymers used in?
Karen: Natural product-derived polycarbonates have applications ranging from single-use packaging and cosmetic microbeads to durable goods.
One significant feature of the current system that is unique from other bioplastics is the diversity of functional groups incorporated into the polymer. These include both carbonates and esters, which are traditionally used in degradable polymer systems, and less commonly used thioether linkages. The sulphur content in the final polymer may impart unique properties that have not yet been explored.
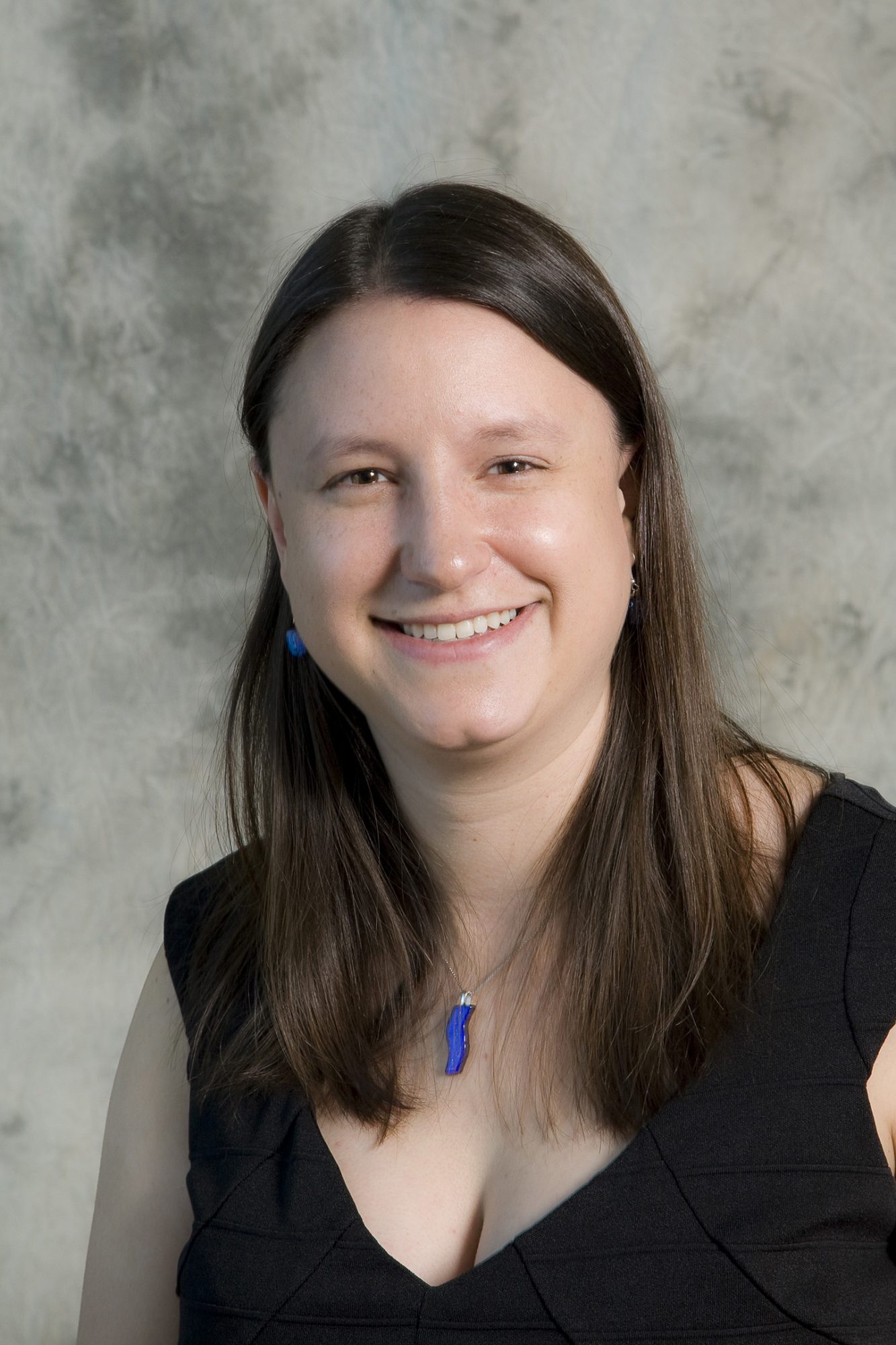
Further, the sugar monomers, which serve as a structural component of the polymer framework, have both alcohol and alkenyl functionalities available for modification, either pre- or post-polymerization, with various chemical groups to impart specifically desired properties to the final polymer system.
About the interviewees
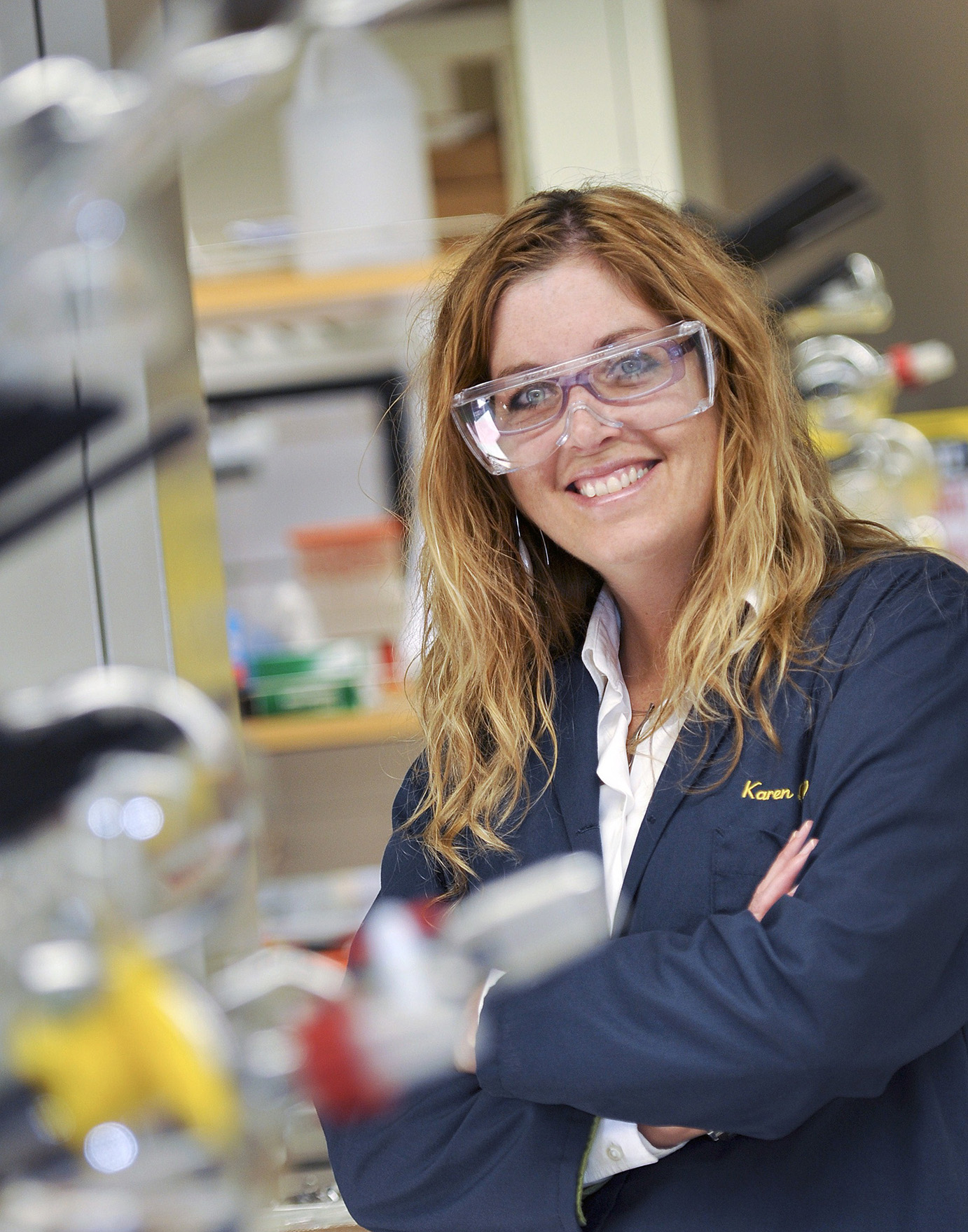
Professor Karen L. Wooley is the inventor and Chief Technology Officer at Teysha Technologies. She is the W. T. Doherty-Welch Chair in Chemistry and a Presidential Impact Fellow at Texas A&M University, where she holds appointments in the departments of Chemistry, Chemical Engineering, and Materials Science and Engineering.
Dr Ashlee A. Jahnke is Project Research Scientist at Teysha Technologies. She was a Colin Hahnemann Bayley Fellow at the University of Toronto, where she received a PhD in polymers and materials chemistry. Her research focuses on natural-product based degradable polymer systems, their scale-up and commercialisation.
Prof Karen L. Wooley
Chief Technology Officer
Dr Ashlee A. Jahnke
Project Research Scientist
Teysha Technologies
Tel: +44 (0)203 856 4029